Getting The Alcast Company To Work
Getting The Alcast Company To Work
Blog Article
The 2-Minute Rule for Alcast Company
Table of ContentsThe Ultimate Guide To Alcast CompanyThe Basic Principles Of Alcast Company The Buzz on Alcast CompanyThe Alcast Company IdeasAlcast Company for BeginnersAll about Alcast Company
Chemical Comparison of Cast Light weight aluminum Alloys Silicon advertises castability by reducing the alloy's melting temperature level and boosting fluidity during casting. Additionally, silicon adds to the alloy's stamina and put on resistance, making it important in applications where toughness is vital, such as auto parts and engine parts.It also improves the machinability of the alloy, making it less complicated to refine into completed products. By doing this, iron adds to the overall workability of aluminum alloys. Copper enhances electric conductivity, making it helpful in electric applications. It likewise enhances corrosion resistance and contributes to the alloy's general toughness.
Manganese contributes to the stamina of aluminum alloys and improves workability (aluminum foundry). It is typically utilized in functioned aluminum items like sheets, extrusions, and accounts. The existence of manganese aids in the alloy's formability and resistance to fracturing during manufacture procedures. Magnesium is a light-weight component that offers toughness and influence resistance to light weight aluminum alloys.
Not known Facts About Alcast Company
It enables the production of light-weight parts with excellent mechanical residential properties. Zinc boosts the castability of light weight aluminum alloys and helps control the solidification process during casting. It boosts the alloy's strength and firmness. It is commonly found in applications where intricate forms and fine details are necessary, such as ornamental spreadings and certain automobile parts.
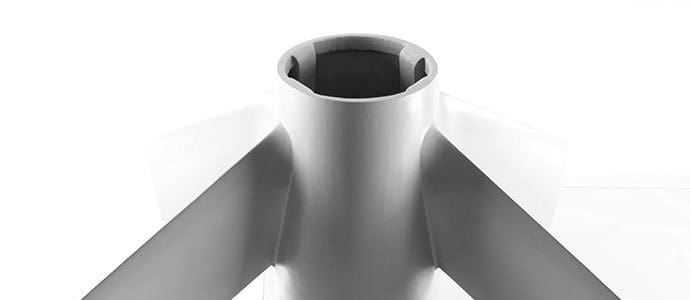
The main thermal conductivity, tensile toughness, return toughness, and prolongation vary. Among the above alloys, A356 has the highest thermal conductivity, and A380 and ADC12 have the most affordable.
The Of Alcast Company
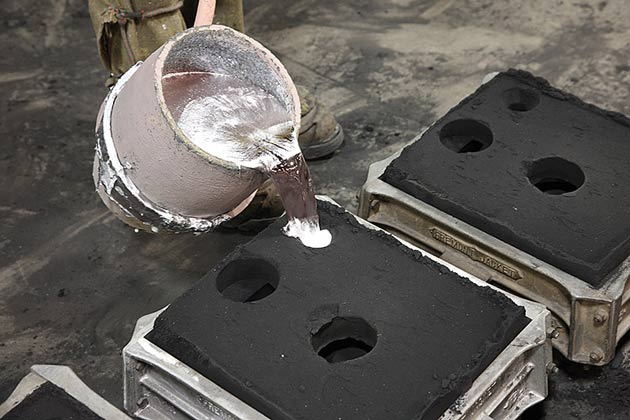
In accuracy casting, 6063 is appropriate for applications where detailed geometries and high-grade surface finishes are vital. Examples include telecommunication rooms, where the alloy's superior formability permits smooth and cosmetically pleasing designs while preserving architectural honesty. Similarly, in the Lighting Solutions market, precision-cast 6063 parts create sophisticated and reliable lighting fixtures that require complex forms and excellent thermal performance.
It brings about a finer surface finish and much better corrosion resistance in A360. The A360 exhibits exceptional prolongation, making it excellent for complex and thin-walled parts. In accuracy casting applications, A360 is well-suited for markets such as Consumer Electronic Devices, Telecommunication, and Power Devices. Its enhanced fluidity allows for elaborate, high-precision parts like smartphone housings and communication gadget real estates.
Fascination About Alcast Company
Its unique properties make A360 a valuable option for accuracy spreading in these markets, improving product longevity and top quality. Aluminum alloy 380, or A380, is an extensively utilized casting alloy with several unique features. It supplies outstanding castability, making it an optimal option for precision casting. A380 displays excellent fluidity when molten, making certain intricate and detailed mold and mildews are accurately replicated.
In precision casting, light weight aluminum 413 beams in the Consumer Electronics and Power Devices sectors. It's typically utilized to craft detailed parts useful source like smart device real estates, cam bodies, and power device housings. Its precision is remarkable, with tight resistances as much as 0.01 mm, ensuring remarkable product setting up. This alloy's superior rust resistance makes it a superb choice for exterior applications, guaranteeing long-lasting, resilient items in the pointed out industries.
Little Known Questions About Alcast Company.
The light weight aluminum alloy you pick will significantly influence both the spreading procedure and the buildings of the last product. Because of this, you must make your decision thoroughly and take an informed approach.
Determining the most ideal aluminum alloy for your application will indicate weighing a wide range of qualities. The first classification addresses alloy features that affect the production process.
The smart Trick of Alcast Company That Nobody is Talking About
The alloy you select for die casting directly impacts numerous facets of the spreading process, like how very easy the alloy is to deal with and if it is vulnerable to casting problems. Hot cracking, likewise called solidification splitting, is a normal die casting issue for aluminum alloys that can result in interior or surface-level splits or fractures.
Certain light weight aluminum alloys are extra vulnerable to hot breaking than others, and your option must consider this. An additional usual flaw located in the die spreading of light weight aluminum is pass away soldering, which is when the actors stays with the die walls and makes ejection hard. It can harm both the actors and the die, so you should search for alloys with high anti-soldering properties.
Corrosion resistance, which is already a noteworthy characteristic of aluminum, can differ substantially from alloy to alloy and is an important characteristic to think about relying on the environmental problems your product will certainly be subjected to (aluminum casting manufacturer). Put on resistance is one more home commonly sought in aluminum products and can differentiate some alloys
Report this page